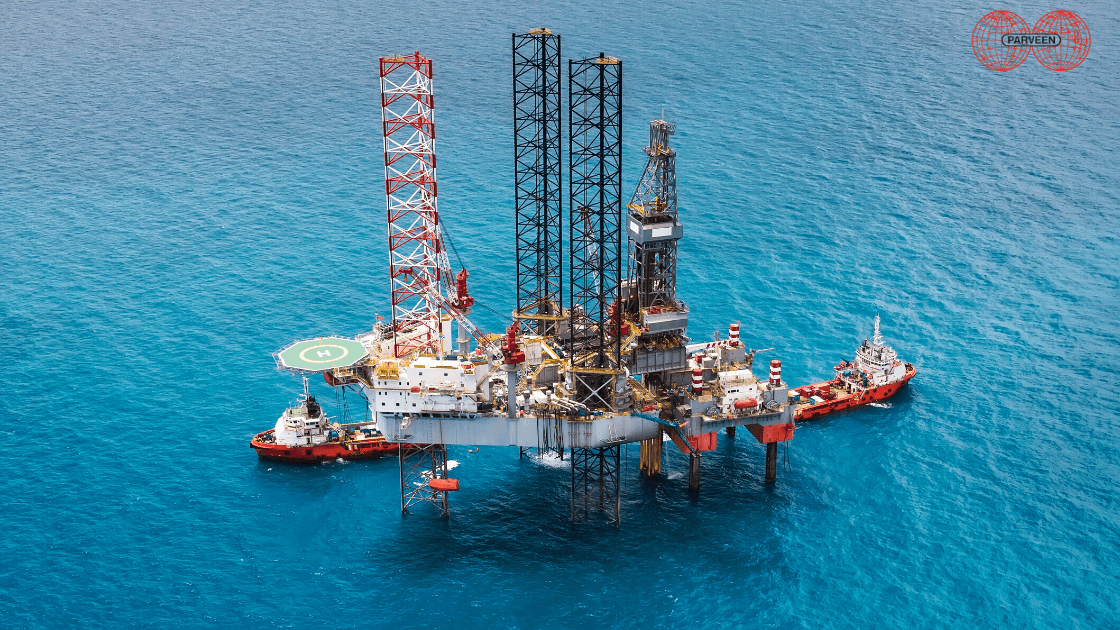
It is imperative for the field operators, pipeline engineers, and designers in the oil and gas industry to be corrosion conscious as the lines and their component fittings would undergo material degradations due to corrosion. And this has a direct impact on productivity.
The annual cost of corrosion to the oil and gas industry in the United States alone is estimated at $27 billion (According to NACE International)-leading some to estimate the global annual cost to the oil and gas industry as exceeding $60 billion. In addition, corrosion commonly causes serious environmental problems, such as spills and releases. An essential resource for all those who are involved in the corrosion management of oil and gas infrastructure, Corrosion Control in the Oil and Gas Industry provides engineers and designers with the tools and methods to design and implement comprehensive corrosion-management programs for oil and gas infrastructures.
Energy Industry has learned to live with corrosion. International Standards Organizations have identified different measures to counter and minimize the effects of this inevitable phenomenon, such as API – RP 583 (Corrosion Under Insulation and Fireproofing) and DNV-RP-C101 (Allowable Thickness Diminution for Hull Structure of Offshore Ships). Usually, two approaches are used in this regard. The first approach involves incorporating for Corrosion Allowance in the design wall thickness of the vessel, pipe or structure and the second one is to use Corrosion Inhibitors. NACE International (formerly National Association of Corrosion Engineers) provides globally recognized standards that are responsive to the latest changes in products and technology, and whose implementation streamlines processes and trims costs. Businesses can prolong the life of their premium assets by following standards such as NACE SP0108-2008 (Corrosion Control of Offshore Structures by Protective Coatings) and NACE TM0194-2014 (Field Monitoring of Bacterial Growth in Oil and Gas Systems).
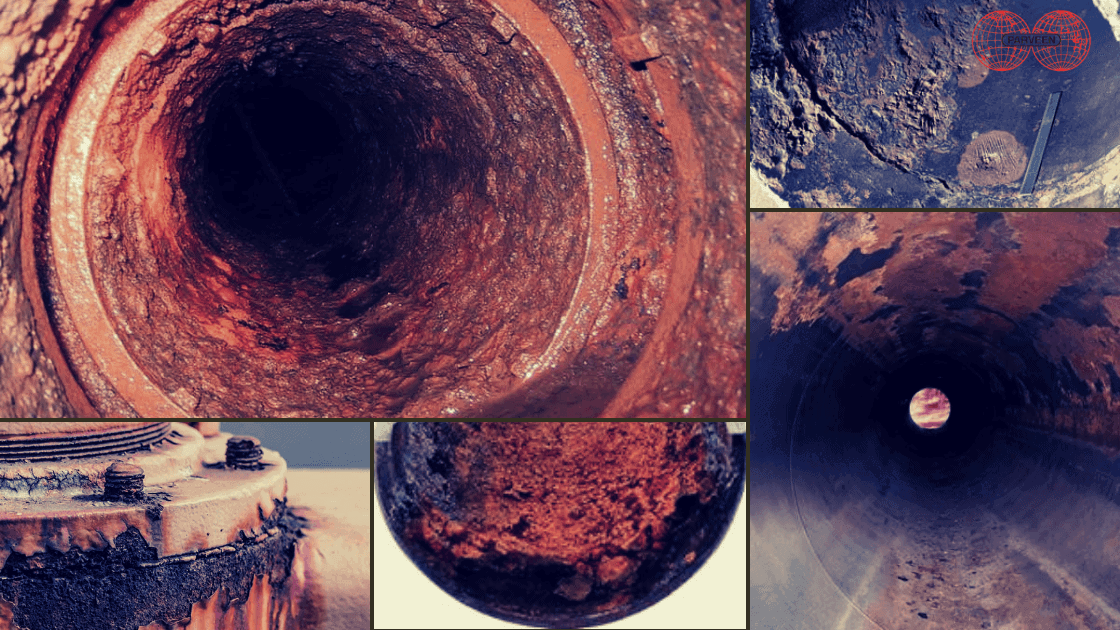
Corrosion Control of Offshore structures requires special attention of designers as well as operators of the facilities. Some of the common types of corrosion in offshore structures are as follows:
General Corrosion:
Where uniform reductions of material are found. Criteria for minimum thickness of hull structural elements may be applied in order to determine average diminution values. Typically, repairs will include steel replacement to original scantlings and/or reinforcement upon special consideration.
Pitting Corrosion:
Random scattered corrosion spots/areas with local material reductions. The intensity of the pitting must first be estimated before applying criteria. Typically, repairs will include the renewal of plates, building up pits by welding.
Grooving Corrosion:
Local line material loss is normally adjacent to welding joints along with abutting stiffeners and at stiffener or plate butts or seams. Due to the complexity and effects of groove corrosion, diminution criteria are limited and special repair considerations are required.
Edges Corrosion:
Local material wastage at the free edges of plates and stiffeners. Typically, if not renewed, repairs may be carried out by means of edge stiffeners/doublers.
Some other common causes are Galvanic, Pitting, Selective attack, Stray current, Microbial, Intergranular, Concentration cell, Thermogalvanic, Combined action, Fatigue, Fretting, Stress cracking, and Hydrogen damage.
Corrosion is not limited to mild steel structures and piping. LNG facilities, which are primarily stainless steel and high alloy materials, the cryogenic process causes large variations of temperature (thermal cycles) thus inducing stresses related to expansion, contraction, bending, and fatigue (expansion and contraction cycles). Additionally, corrosion becomes a serious concern with the passage of time which includes pitting corrosion as well as stress corrosion cracking. The subtle danger with stainless steel is that the corrosion may not be recognized until the component starts leaking.
LNG steel tanks require regular inspection for bottom grouting between the outer bottom footer plate and the ring wall for any evidence of leakage or corrosion, for anchor straps for corrosion at the concrete ring wall / platform interface, for frost spots on the outer surfaces, as these would indicate a loss of insulation performance in the annular space. Infrared imaging of the tank would detect this condition and this can be easily carried out through drone-mounted IR cameras.
Surface corrosion can be easily detected but Corrosion Under Insulation (CUI) is difficult to.
In the absence of scheduled NDT inspections, the condition of piping and fitting is largely unknown to the plant manager. As required under API, CSA or ANSI standards/guidelines as well as for compliance under EPA regulations it is a must in today’s business environment to watch out for corrosion. Most rupture and leakage incidents in the Oil & Gas industry are related to metal loss as a result of corrosion, mechanical creep over time or mechanical damage caused by external or internal factors. Neglect in this area leads to the imposition of heavy fines and a company may also get involved in damage recovery suits. Oil spills from a storage tank or transport pipeline leakage may cause severe or irrecoverable damage to the environment.
To know how our support solutions can help increase your productivity with proper maintenance support write to us here.
Acknowledgments
Parveen Industries Private Limited would like to acknowledge that our authors have referred various articles, white papers, scientific studies and research work for the compilation of this blog.